Difference between revisions of "Projets:Perso:2020:CharlyIsel"
(→No risk, no fun) |
(→No risk, no fun) |
||
Line 365: | Line 365: | ||
− | [[File:Alim_filtre.JPG|right|500px|thumb|Montage à blanc du filtre secteur (un grand merci à Christian pour la richesse de ses fonds de tiroir) et de l'alimentation 24V "permanente". Cet ajout implique un déplacement des deux rails DIN et un léger toilettage du câblage qui, avec le temps est les multiples modifications, tend à se transformer une pelote inextricable]] | + | [[File:Alim_filtre.JPG|right|500px|thumb|Montage à blanc "non fixé" du filtre secteur (un grand merci à Christian pour la richesse de ses fonds de tiroir) et de l'alimentation 24V "permanente". Cet ajout implique un déplacement des deux rails DIN et un léger toilettage du câblage qui, avec le temps est les multiples modifications, tend à se transformer une pelote inextricable]] |
Revision as of 07:43, 15 April 2021
Retrofit de CNC CharlyRobot génération Isel
Contents
- 1 Pour qui, pourquoi ?
- 2 La logique de contrôle
- 3 Opérations de maintenance
- 4 Changement de La Vis à Billes des X
- 5 Modification du porte broche
- 6 Electronique de commande
- 7 Retrofit du retrofit:
Pour qui, pourquoi ?
Pour tous ceux qui n'ont pas la patience de plancher sur un hypothétique cahier des charges, lequel de toute manière ne saurait être défini puisque reposant sur le principe de la permanence des choses...
Pour ceux, également, qui ont mis la main sur une de ces nombreuses machines achetées par l'Education Nationale et qui se retrouvent sur le marché des "secondes mains".
Pour ceux, enfin, qui ne possèdent pas le moindre iota de connaissance mécanique et qui sauront supporter les approximations et trahisons de l'auteur.
La logique de contrôle
Ce projet est en fait le résultat d'une confluence : l'arrivée inopinée d'une fraiseuse CNC Proxxon d'occasion vendue à faible prix (et spottée par F4GRX, qu'il soit béni) et la découverte, toujours pour un prix plus qu'attractif, d'un châssis de Charlyrobot motorisation et structure Isel. Les deux projets, chacun à un stade différent, seront menés de front compte tenu de la similitude des opérations à conduire. Une description de modernisation d'un châssis strictement identique se trouve sur le forum Usinages
Une première électronique de pilotage destinée à la fraiseuse Proxxon est en cours de construction, et sert de projet préparatoire avant l'attaque du "gros" chantier Charly.
Sur les conseils de Sebastien, il a été décidé d'éviter dans un premier temps les logiciels de pilotage complexes tel que LinuxCNC, mais plutôt de partir sur une solution simplifiée reposant sur grbl et l'interface/transmetteur de Gcode "bCNC".
Afin de faciliter les premiers pas avec ce logiciel, quelques "recettes" d'utilisation ont été rédigées en Français
Cette documentation sera enrichie au fil du temps Le premier chapitre disponible explique comment étalonner le repère Z=0 et gérer le changement d'outils au cours d'un même usinage .
C'est, de loin, l'approche la plus économique et surtout la plus rapide, car elle existe déjà quasiment prête à l'emploi grâce à une entreprise Australienne, Protoneer.
Celle-ci commercialise une carte open hardware, open source à base de microcontroleur Atmel (lequel est chargé de supporter grbl) et qui se monte en "piggy back" sur un SoC Raspberry-Pi.
Un Raspi qui fait tourner l'un des logiciels de contrôle sous Linux Raspbian tel que bCNC, ou joue le rôle de serveur d'administration/contrôle à distance via un service Web et une interface html.
Toute la documentation de ce Raspberry Pi CNC Hat estaccessible sur le Wiki de Protoneer.
Sur cette carte viennent se brancher des drivers genre Pololu. Si l'on envisage de commander des moteurs pas à pas plus puissants, une série de "jumpers" imprimés routent les signaux de commande vers des modules externes, tels que ces DQ542MA pouvant débiter 4 ampères par phase de manière ponctuelle (3A RMS)
L'électronique Protoneer supervise :
- 3 ou 4 pilotes de moteurs pas à pas sur 3 axes (le quatrième moteur se limitant à recopier l'un des 3 axes principaux)
- L'activation et la direction de la broche si celle-ci n'est pas indépendante
- 3 circuits pour les interrupteurs fin de course pour chaque axe
- Le déclenchement d'un circuit de refroidissement -ou d'une microlube-
- Les commandes manuelles d'urgence Abort, Hold, Resume et Reset/Restart (Hold et Resume étant nécessaire lors de chaque changement d'outil)
La logique de contrôle peut donc se résumer à :
- Un micro-ordinateur Raspberry Pi chargé d'exécuter le logiciel de commande d'usinage et assure l'interface Homme/Machine (UHM)
- Une carte Protoneer avec son simili-Arduino Nano qui récupère les commandes Gcode et les traduit en commandes d'actuateurs (moteurs pas à pas, électrovannes, relais marche/arrêt, capteurs de fin de course etc)
- 3 ou 4 drivers de puissance pour moteurs pas à pas
- Une alimentation 5V 4A destinée à alimenter le Raspberry et sa carte Protoneer
- Une alimentation de puissance 24 V 10 ou 12 ampères qui fournira l'énergie nécessaire aux moteurs X, Y et Z
- Un écran HDMI, un clavier, une souris (IHM)
Plus spécifiquement pour le projet CharlyRobot :
- Une alimentation de puissance consacrée à la broche
- Une petite pompe à air destinée à la micro-lubrification de l'outil en cours d'utilisation
Opérations de maintenance
(opérations effectuées à ce jour)
- Nettoyage du châssis
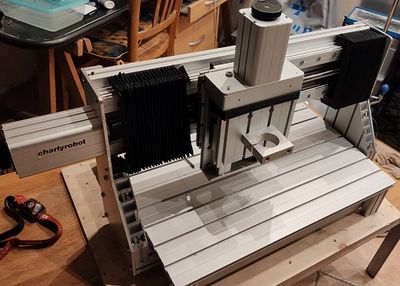
- Démontage, restauration et remontage des soufflets
- Rectification des "impacts" de broche sur la table, vérification de la planéité au comparateur
- Dégraissage des résidus (acétone, essence F, brosse à dents) qui dataient de plus de 30 ans et formaient une gangue solide sur toute les mécaniques de translation
- Graissage des Vis à Billes et rails cylindriques
- Contrôle des jeux et des déplacements. L'axe des X "gratte" dans le sens lévogyre, à la limite du blocage
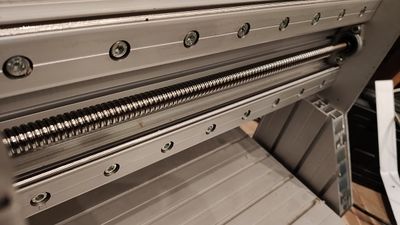
- Démontage de l'ensemble X / Z, dépose de la VaB des X, démontage de la noix, nettoyage, rebillages successifs avec des billes roulées neuves. Cette noix contient trois circuits de billes, et l'un des circulateur, trop usé, est responsable du grippage. Les deux autres circuits ne sont plus très vaillants non plus
- Rebillage final de l'axe des X avec seulement 2 circuits de billes, en attendant la commande d'une noix Hi Win de remplacement (l'histoire nous apprendra qu'il s'agissait là d'une douce illusion)
- Changement des paliers de l'axe des X d'origine Isel, totalement excentrés d'origine, vérification des axez Z et Y
(opérations prévues)
- Remontage -provisoire- de l'axe des X, du bloc Z, des pièces de capotage, et rebillage éventuel des roulements de rails
- Remontage du capotage
- Remontage des moteurs d'origine, qui seront peut-être à terme remplacés par des Nema 23 de plus forte puissance
- Usinage du porte broche 1kW (à terme. Provisoirement, un moteur 500W jouera les mulets)
- Construction/assemblage de l'électronique de commande (grbl/arduino/raspberry) intégrant les drivers 3 axes, la commande de microlube, les alimentations au même standard de branchement que l'électronique de la Proxxon
Changement de La Vis à Billes des X
Bien entendu, impossible de trouver une vis à bille Hi-Win adaptable sur le chassis Isel. Après moultes errements allant de la tentative de rebillage à la modification d'une VaB Chinoise, il a bien fallu se résoudre à commander une vis "sur mesure".
Le sous-traitant choisi est Tuli, en raison de sa proximité et de la réactivité de son service client. Les tarifs sont... confortable mais justifiés. 40 euros de noix à triple circulation, 60 euros de vis à bille... mais 130 euros d'usinage à façon. On est très en deçà des tarifs SKF ou Rexroth, très au dessus des productions Chinoises.
- Premier écueil, il n'existe pas de noix avec un pas identique à celle d'origine pour une vis de cette longueur. De 16x4, il a fallu passer à 16x5 (simple ajustement logiciel au niveau du contrôle de la machine). La modélisation de la Vis à Bille et de sa noix sous FreeCAD a été grandement facilité par l'importation directe d'un modèle de la noix au format STL, disponible sur le site du fabricant
- Après mesures, la nouvelle noix Tuli rentre "tout juste" dans le chenal de l'axe des X, mais butte sur les mâchoires des guides à bille linéaires. Ce problème a nécessité de monter la noix "à l'envers" du montage originel.
- En outre, le diamètre de la noix étant plus important que celui de la pièce d'origine (29mm contre les 26mm), il a fallu usiner un nouveau porte-noix fileté en M25 ISO.
- Second écueil : Le probable responsable de l'usure de la noix semble être l'alignement peu orthodoxe de la vis avec ses roulements d'extrémité, lesquels roulement d'origine ne sont pas franchement coaxiaux
- Troisième écueil : les supports en fonte d'aluminium, doivent être rôdés pour que le roulement puisse se positionner dans l'axe de la vis. Sans un léger passage à la toile Emery, il est impossible d'aligner les extrémités d'arbre et les moyeux. L'arbre lui-même a dû être très légèrement rôdé (abrasif 1000). Le rodage doit être très léger, pour ne pas créer de jeu entre la vis à bille et le moyeu du roulement, et entre le roulement lui-même et son support
Le remontage s'effectue dans l'ordre inverse de dépose :
- Nettoyage et graissage des 8 roulements linéaires, rebillage de deux d'entre eux avec des billes neuves
- Insertion de la vis à bille dans son chenal
- Glissement de chaque extrémité de la VaB dans les moyeux des roulements d'extrémité
Montage de la vis Tuli et sa noix dans le chenal de l'axe X : tout rentre exactement à sa place, sans le moindre jeu.
- Vissage sans serrage des vis de fixation des roulements
- Vissage du porte-noix sur le chariot du porte broche, avec contrôle au comparateur du parallélisme du corps de la noix et des rails de guidage linéaire
- Serrage des vis des roulements en prenant garde à ne pas contraindre la vis à bille
- Pose du circlip de blocage coté moteur
- Pose de l'écrou de blocage sur l'autre extrémité
- Serrage des blocages de moyeu (vis 6 pans creux sans tête) sur chaque roulement
Ces opérations effectuées, il ne devrait y avoir aucun jeu latéral de l'axe des X, la noix doit se déplacer sans effort d'une extrémité à l'autre.
Modification du porte broche
Le diamètre de la broche provisoire 500W est de 52mm, le support de broche d'origine est de 42mm. L'écartement des fixations du nouveau porte broche est incompatible avec l'espacement des gorges du profilé situés sur le chariot de l'axe Z.
"Broche provisoire" car la tenue mécanique de ce moteur est... au mieux "très relative" (pour 20 euros alimentation comprise, il ne faut pas s'attendre à un modèle du genre, le centrage du moteur étant assuré par un joint torique en caoutchouc), mais amplement suffisante pour effectuer les premiers essais.
Pour contourner ce problème sans modifier la structure du chariot, il a été décidé d'ajouter une plaque intermédiaire de profilé 20x20 (quadruple rails). Le choix du rail 20x20 est dicté par l'écart vertical entre les vis M6 de fixation du support de broche (2 cm)
Cet ensemble est alésé et taraudé au format du porte-broche, et 4 autres alésages M6 situés proches des 4 coins de la plaque servent à faire passer les vis de fixation de ladite plaque à l'aplomb des rails en T du chariot (espacement de 50)
Electronique de commande
Réalisé dans un rack "de récupération", cette centrale de commande est la copie conforme du contrôleur réalisé pour la fraiseuse Proxxon :
- Chapeau Protoneer pour Raspberry Pi (3B+),
- drivers de puissance,
- alimentation 24V 15 (une 36V eût été préférable... si vous vous aventurez sur un tel chemin, optez pour la tension la plus élevée possible, compatible avec la tension de service de vos drivers)
- alimentation 5V pour le Raspberry Pi. Si possible de qualité (MeanWell si votre budget le permet)
- alimentation du moteur de broche (provisoire)
- interface de contrôle de moteur de broche (M/A, direction et conversion PWM vers 0-10V "mach3" style, soit un pcb original pondu sous Kicad, soit une verrue à base de récupération et détournement de carte P0wArduino)
- sortie vidéo pour écran de contrôle Pi-CNC
- IHM de base (Restart/Resume/Hold/Abort et réglage du Z, voir les fournisseur de boutons "Jacky's tuning" étanches et solides)
- si résultats concluants, une microlube à base de compresseur d'aquarium ou ensemble compresseur/aérographe modifié.
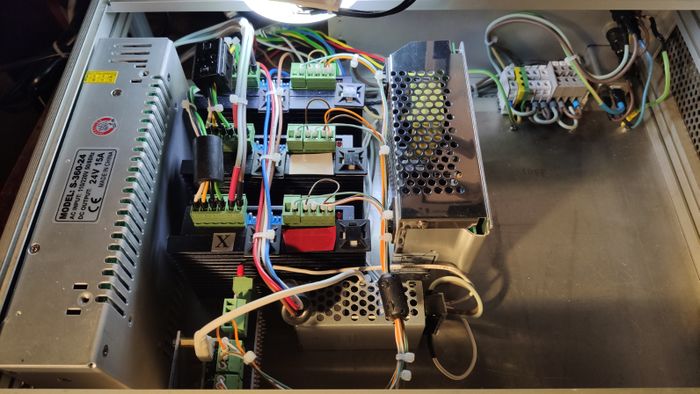
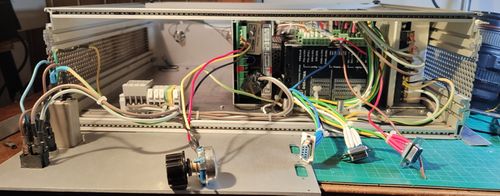
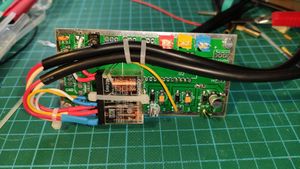
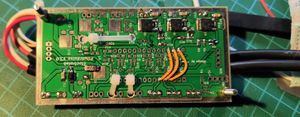
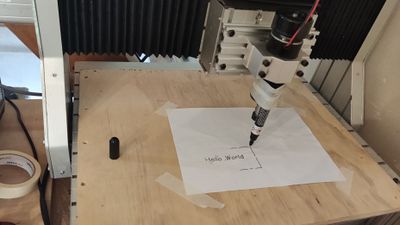
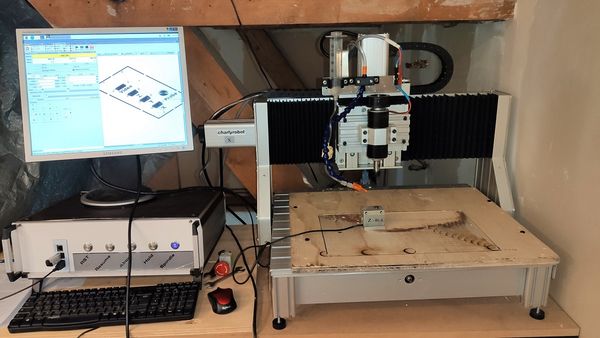
Retrofit du retrofit:
Cette première phase achevée, la machine-outil est configurée, testée et mise en service. Très rapidement, l'ubris du monteur et quelques usinages ont incité à accroitre la puissance de l'ensemble. Une sorte de "CNC de Jackie" en quelques sortes.
l’étape suivante consiste donc à installer une broche un peu plus puissante. Le moteur choisi développe 2.2 kW de puissance refroidie par liquide, mais une 1.5 kW aurait mieux convenu. Ses principaux avantages :
- Refroidissement liquide qui fonctionne y compris à basse vitesse, contrairement au refroidissement « air » qui est moins efficace lorsque le ventilateur tourne trop lentement
- Vitesse d’usinage plus rapide, à 24 000 tm, contre 10 000 pour la broche 500W
- puissance plus adaptée au travail du métal
Ses principaux inconvénients :
- Un poids de près de 9 kg qui sollicite plus l’axe Z et les moteurs pas à pas X et Y
- Un circuit de refroidissement relativement lourd, encombrant et compliqué
- Nécessité d’usinage d’une plaque intermédiaire pour fixer l’étau du moteur de broche et la plaque de l’axe Z
- Nécessité d’utiliser un convertisseur mono vers triphasé à fréquence variable -100 à 400 Hz-, qui pilotera le moteur de broche (vitesse, gestion des temps de mise en rotation et freinage, sens de rotation). Ce convertisseur (VFD) est un périphérique programmable nécessitant un paramétrage en fonction du moteur de broche d’une part, et des ordres envoyés par bcnc d’autre part
- Considérablement moins de tolérance à l’erreur, risques de casse proportionnels à l’accroissement de puissance
Usinage de la semelle d’étau de broche
Cette plaque d’aluminium de 15mm d’épaisseur est percée de
- 8 alésages pour vis BTR M6 qui viennent fixer la plaque sur le chariot de l’axe Z, chaque trou étant fraisé pour noyer la tête de vis dans la masse
- 6 alésages perpendiculaires aux premiers pour autant de vis BTR M6 destinées à fixer l’étau de broche, avec un chambrage de tête identique mais situé sur l’autre face de la plaque
Cette plaque a été dessinée sous Freecad, la traduction en gcode est l’œuvre de CamBam et la pièce a été usinée avec la broche 500W, fraise monoflute de 3mm de diamètre.
Modification des chaines de tirage
La chaine de tirage initialement installée le long de l’axe X s’est avérée bien trop étroite pour contenir le câble d’alimentation triphasé (blindé, plus conséquent que le « monophasé 100V » du moteur 500W), les tubes aller et retour du circuit de refroidissement, et le tube d’air sous pression de la microlubrification. Elle est remplacée par une chaine 50x20mm à maillons ouvrables. Cette chaine repose en grande partie sur la face supérieur du portique
Une seconde chaine est également installé sur le chemin de l’axe Y, qui ne supporte que les câbles d’alimentation des moteurs pas à pas X et Z. Cette chaine est soutenue par une cornière en aluminium, elle-même fixée sur le châssis de la machine.
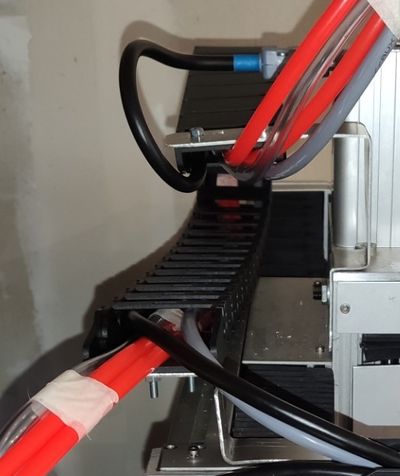
Panneau arrière de support VFD, refroidissement hydraulique, lubrification
Très souvent, les retrofits de CNC portique utilisent l’arbre horizontal du portique pour supporter les périphériques accessoires. Mais la masse du moteur de broche étant déjà assez conséquence, il a été décidé de regrouper ces périphériques sur un panneau fixe, solidaire du châssis de la machine-outil. Le panneau est découpé dans une feuille d’aluminium boulonnée sur trois cornières également en aluminium, elles-mêmes vissées sur les empiètements et le plateau de la CNC. La plaque est doublée d’une couche de stratifié (imitation bois du plus bel effet), collée sur la plaque alu. Le sandwich aluminium/colle silicone/stratifié amorti sensiblement les vibrations de la machine.
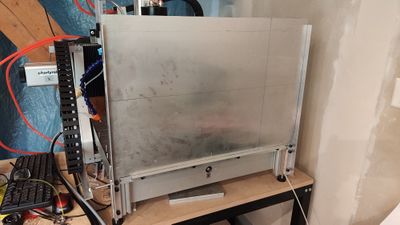
Circuit de refroidissement
Un premier tuyau de 6mm de diamètre relie le moteur de broche à une pompe « haute » alimentée en 12Vcc, qui refoule le liquide de refroidissement dans un échangeur de chaleur (radiateur équipé de deux ventilateurs également alimentés en 12V). Le liquide refroidi s’écoule ensuite dans un réservoir tampon d’une contenance de 400 ml. Ce réservoir est solidaire d’une seconde pompe qui expédie à son tour le liquide dans le moteur de broche. Le volume totale de liquide circulant dans le réservoir, la tuyauterie, le radiateur, le corps de broche et les moteurs de pompe avoisine les 700 ml. La longueur totale de la tuyauterie s’approche des 5 mètres La tension de 12V utilisée par les deux pompes et les deux ventilateurs est fournie par une alimentation à découpage, elle-même branchée au panneau arrière du rack de commande
Circuit de lubrification
Il se limite à un seul élément : la pompe à air à basse pression. Il s’agit d’une pompe pour aquarium intégrant deux pompes doubles à membrane -soit 4 sorties-. Ces sorties sont reliées entre elles par une buse et routée via un tuyau de 6mm vers l’injecteur à effet venturi maintenu en extrémité d’une loc-line. Le réservoir d’huile de coupe, fixé sur le chariot de l’axe X, fonctionne par gravité. Le débit est réglé par un robinet de « goutte à goutte » médical. L’ensemble de ce système de microlubrification basse pression est commercialisé par CNC Fraises et conçu par The Breizh Maker
VFD:
Sur le bloc VFD partent 4 câbles : Le 220V triphasé 100/400 Hz à fréquence variable en direction du moteur Le 220V monophasé 50 Hz d’alimentation (activé ou non à partir du rack de commande) Un faisceau de câbles de contrôle de vitesse -0/10V- et sens de rotation, également relié au rack de commande.
Modification du rack de commande
Le bloc d’alimentation à tension variable 0/100V du moteur 500W est enlevé La logique de contrôle de sens de rotation et de conversion pwm/0-10V est remplacée par une carte d’interface à 4 relais, un module dédié de conversion PWM/ 0-10V plus efficace, un convertisseur de tension step down qui transforme une tension 24V en 11V qui alimentera à son tour le convertisseur pwm mentionné. Les relais sont directement pilotés par la carte Protoneer. Un premier relais assure l’inversion du sens de rotation, un second relais récupère la commande de microlubrification et excite un second relais, plus puissant, qui à son tour alimente en 220V la sortie sur laquelle vient se brancher la pompe basse pression. L’activation du moteur de broche est commandée par un bouton-poussoir en façade du rack de commande (ce qui ne change rien au mode de fonctionnement précédent). Ce bouton ferme un circuit 24V qui vient activer le relais de puissance qui alimente le VFD Les différents borniers de répartition du courant secteur, les relais de puissance et le bornier de la tension de service 24V sont fixés sur des rails DIN.
Le panneau arrière a également été usiné pour supporter
- L’entrée générale 220V sur connecteur IEC20, 4 sorties 220V permanente sur IEC14 (refroidissement broche/circuit hydraulique, moniteur vidéo, éclairage de la table d’usinage),
- Deux IEC14 de sortie « alimentation du VFD », commutée par relais interne « moteur on »
- Deux IEC14 de sortie relais « microlube », commutées par la carte Protoneer et bcnc, dont une prise pour le compresseur, l’autre pour une éventuelle électrovanne de lubrifiant (non encore installée)
- Une sortie dB15 de commande logique de rotation de broche (vers le boitier VFD)
- Un inter M/A qui ferme un circuit 24V (tension permanente dès que le connecteur IEC20 est branché) et excite un relais de puissance général 20 A monté sur rail DIN.
No risk, no fun
Les premiers essais se sont soldés par un échec cuisant. A chaque interruption du relais de commande de la microlubrification, bcnc se mettait en rideau, avec une alerte majeure invoquant un déclanchement de sonde de fin de course ou du capteur de Z. Une rapide mesure à l’oscilloscope montrait la présence d’une impulsion transitoire assez prononcée sur le rail 5V alimentant le Raspberry Pi.
Après avoir progressivement « dégraissé » toute la circuiterie microlub, ajouté un condensateur de 4700 uF sur le 5V, découplé la bobine du relais 220V avec une 100nF, le canard était toujours vivant. En continuant de remonter le signal de commande, il a bien fallu se rendre à l’évidence que la carte « multi-relais » de premier niveau (celle directement branchée à la carte Protoneer) ne possédait strictement aucune capa de filtrage aux bornes des bobines. Une paire de capa 100nF/10nF sur chaque composant et un tantale de 3.3uF sur l’entrée 5V a résolu la question.
Un filtre secteur conséquent (30A) et une alimentation d’amorçage 24V (mise sous tension générale commandée par relais) ont également été ajoutés après coup. Pour isoler l’électronique de commande de parasites provenant du courant secteur, et pour éviter d’injecter trop de perturbations générées par les commutations diverses et le VFD.
Extensions qu'il reste à monter
- Un bouton d'arrêt d'urgence
- Un tiroir à glissière situé sous la CNC pour y loger le boitier de commande, le clavier, la souris...
- Un râtelier à fraises
- A plus longue échéance, le remplacement des moteurs pas à pas par des servomoteurs, en d'autres termes, élimination de l'alimentation 24V de puissance pour un bloc 50V (alimentation de serveur ou gros routeur) suppression du "hat" Protoneer pour un contrôleur à base de fpga genre carte Mesa, et pilotage via LinuxCNC.